Luca Inzerillo 22 maggio 2012
Uno studio realizzato negli anni novanta da Whittaker e Frith fa risalire ai tempi più remoti della storia dell’uomo la pratica di costruire gallerie: una galleria mineraria dello Swaziland è stata datata addirittura al 40000 a.C.!
Oggi l’uomo realizza ogni sorta di gallerie ed opere sotterranee, attraversando ogni tipo di terreno, dai tunnel transalpini a quelli sottomarini. Tra tutte queste dobbiamo ricordare: la prima galleria ferroviaria (Liverpool – Manchester, 1826-1829), la prima galleria subacquea (Londra, 1842), il primo traforo alpino (Frejus, 1857-1870) e la prima galleria sottomarina (Seikan, 1964-1983).
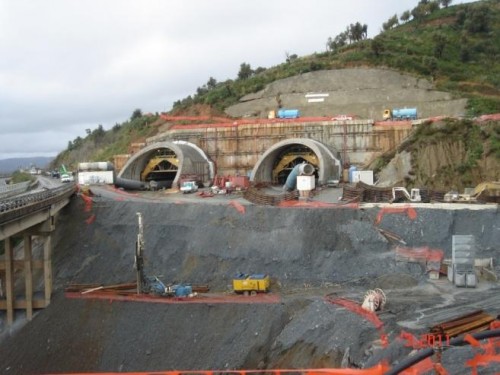
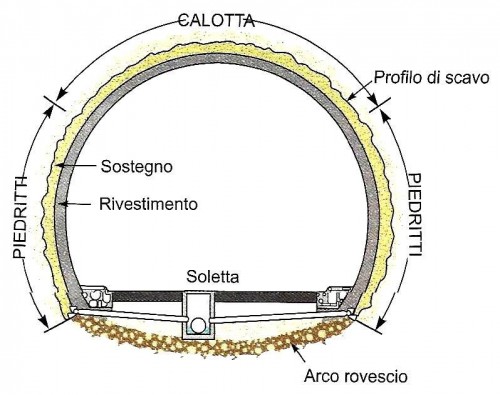
Pur essendo opere rischiose e complicate, gli innumerevoli vantaggi derivanti dalla realizzazione di un tunnel hanno spinto e tuttora spingono l’uomo ad investire ingenti risorse, economiche e materiali, per la costruzione di queste grandi opere; per esempio nel caso dei collegamenti viari, specie se transalpini, la riduzione delle distanze, la maggiore velocità ed i minori tempi di percorrenza sono sicuramente tra i maggiori vantaggi derivanti da questo tipo di soluzione rispetto ad un tracciato di superficie; per migliorare il trasporto pubblico, eludendo il traffico privato, realizziamo moltissime metropolitane nelle nostre città. Soluzioni in galleria sono state scelte per la realizzazione di condotte idrauliche, sia a scopo energetico (centrali idroelettriche) che ambientale (l’Adda è stato trasferito in galleria per bypassare la gigantesca frana della Val Pola del 1987). Infine siti sotterranei sono da preferire per lo stoccaggio di alcune materie pericolose (ordigni e/o scorie nucleari).
Attualmente in Europa, attraverso la barriera delle Alpi, sono in progetto o in corso di realizzazione diversi tunnel ferroviari detti “di base” (per esempio: Brennero, San Gottardo, Val di Susa): queste gallerie, molto più lunghe di quelle esistenti attraverso le Alpi, sono mosse dal principio per cui diminuendo la quota del traforo, diminuiscono le pendenze, si rettifica il tracciato e quindi si realizza un collegamento più veloce e, a parità di mezzo di trasporto, meno dispendioso energicamente e quindi meno inquinante.
Una progettazione attenta servirà a prevenire gravi inconvenienti, sia per la sicurezza degli operai, sia per quella degli utenti, sia per quella ambientale: infatti l’ambiente sotterraneo non è conosciuto e caratterizzabile allo stesso modo di come si può fare per un lavoro in superficie. Almeno finché non è iniziato lo scavo ed è possibile osservare dall’interno il mondo sotterraneo. La possibilità di incontrare acque sotterranee bollenti (idrotermali) o ad alta pressione (falde acquifere) è sempre in agguato, così come quella di attraversare rocce deboli o così fratturate che possono crollare. Inoltre una galleria può essere responsabile di gravi disastri ambientali, semplicemente drenando enormi quantità d’acqua e prosciugando le fonti delle montagne o delle valli circostanti. Il drenaggio a sua volta può causare grandi cedimenti nel terreno (subsidenza) e danneggiare le case e gli edifici che vi sono costruiti al di sopra.
Ma come si scava una galleria??
Esistono due grandi metodi per lo scavo in sotterraneo: lo scavo tradizionale e lo scavo meccanizzato.
Il primo metodo è quello “classico” che utilizza l’esplosivo per avanzare nell’ammasso roccioso; è anche noto come N.A.T.M. (New Austrian Tunnelling Method) ed è stato sviluppato intorno agli anni ’40 da Rabcewicz in base ad alcune osservazioni sul comportamento degli ammassi rocciosi e sulla relazione esistente tra tipo di sostegno utilizzato e la deformazione radiale subita dal cavo. Lo si può applicare in tutti i tipi di terreno (dalla terra alla roccia dura) e consiste nell’esecuzione ciclica di diverse operazioni che permettono di avanzare lungo il tracciato:
- Realizzazione del pre-sostegno del fronte di scavo (solo per terreni e fronti instabili)
- Perforazione e carica della volata (si realizzano con un macchinario chiamato Jumbo, una serie di fori con una precisa geometria e si riempiono di esplosivo. Sia la disposizione dei fori che la quantità d’esplosivo sono calibrate in modo da far cedere la porzione di roccia desiderata e di non creare “danni” alle porzioni di roccia che faranno da sostegno naturale allo scavo)
- Il materiale abbatuto (detto smarino) deve essere rimosso con delle ruspe e dei camion
- Lo scavo viene sostenuto con la realizzazione di bulloni e calcestruzzo proiettato
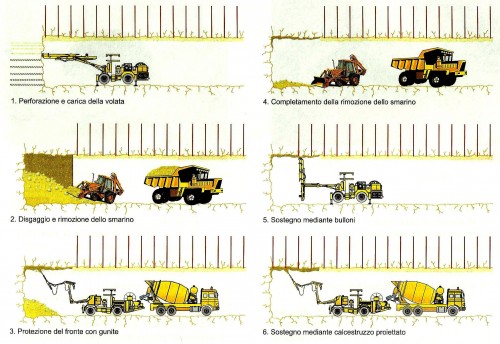
Il cuore del metodo è insito nell’abbattimento della giusta porzione di roccia, così da realizzare al contorno dello scavo (cioè sulla roccia) una ri-distribuzione delle forze nota come effetto arco che, almeno in parte, si prenderà carico del “peso” della montagna; sarebbe impossibile, altrimenti, sostenere lo scavo solamente con ferro e cemento!! Dopo poco tempo la galleria si chiuderebbe da sola!
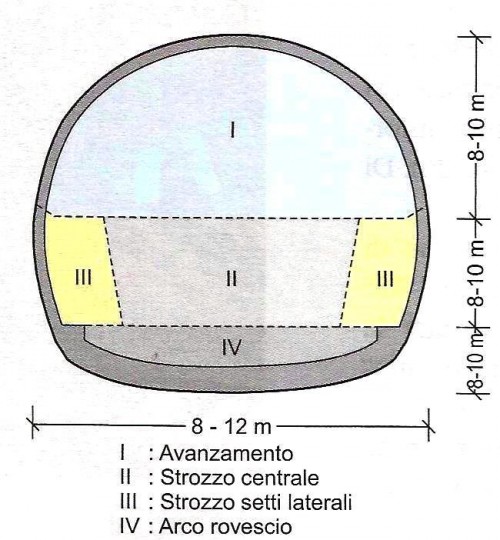
Generalmente, non si scava l’intera sezione della galleria simultaneamente, ma si procede per gradi, cominciando dalla volta e procedendo verso il basso. L’ultima operazione svolta è la realizzazione dell’arco rovescio, ovvero la trave curva che sta alla base della galleria e che ha la funzione di chiudere l’arco di cemento armato già realizzato e di farlo lavorare al meglio. Questo perché una sezione circolare che lavora “chiusa” come un tubo permette di distribuire gli sforzi meglio di una sezione costituita da elementi separati tra loro. Inoltre permette di far lavorare il calcestruzzo armato molto meglio perché lo fa lavorare a compressione, cioè schiacciandolo, e non a trazione o flessione, cioè tirandolo o piegandolo; questo tipo di materiale, così come le rocce, resiste molto di più alla compressione (almeno 10 volte di più) che non agli altri due sforzi.
Il secondo metodo consiste nello scavare la galleria con dei mezzi meccanici. Per comprendere l’argomento occorre fare due grandi distinzioni: prima di tutto se lo scavo avviene per sezioni parziali (come nel caso delle gallerie in tradizionale) o a piena sezione (cioè scavando l’intera sezione della galleria tutta nello stesso momento). Nel primo caso si procederà all’incirca come già descritto per il metodo tradizionale con delle frese puntuali e con dei demolitori (al posto dell’esplosivo), realizzando per gradi la sagoma della galleria che sarà successivamente rivestita con il calcestruzzo armato.
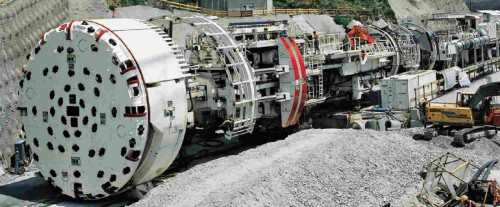
Nel secondo caso l’avanzamento sarà realizzato con una complessa macchina detta TBM (Tunnel Boring Machine), nota anche come fresa o talpa, che oltre ad eseguire lo scavo è in grado di sostenere ed evitare i cedimenti del fronte di scavo, di portare all’esterno lo smarino (tramite un nastro trasportatore) e di mettere in opera il rivestimento definitivo che questa volta è costituito da conci prefabbricati in calcestruzzo armato.
Questo tipo di macchina è in grado di scavare nella quasi totalità dei contesti geologici esistenti (da qui la seconda distinzione), dalla roccia compatta (hard-rock TBM) a quella fratturata (double-shield TBM) fino ai terreni sciolti ed al di sotto della falda acquifera (EPB – Earth Pressure Balance machine).
Adesso cerchiamo di capire com’è fatta una TBM e come funziona; le parti fondamentali sono sempre le stesse anche se esistono delle “piccole-grandi differenze” tra le varie macchine e cercherò di farvele notare.
Cominciamo dalle cose in comune e dai principi generali; tutte queste macchine hanno, come elementi principali:
- Una testa, cioè la parte anteriore a diretto contatto con il fronte di scavo, che serve a scavare, sostenere il fronte, raccogliere e convogliare lo smarino verso un sistema di evacuazione
- Un sistema di trasporto dello smarino verso l’esterno della galleria (p. es. un nastro trasportatore)
- Diversi motori (elettrici) ed un sistema di propulsione che serve a far girare la testa e a spingere avanti la macchina (in genere con dei pistoni idraulici)
- Un sistema di messa in opera del rivestimento della galleria, qualunque esso sia
- Diversi carri di back-up, cioè delle strutture che viaggiano al seguito della fresa vera e propria e contengono tutti gli strumenti necessari per le operazioni di scavo e costruzione della galleria.
Qui sotto c’è uno schema abbastanza dettagliato di una TBM double-shield. Ecco come funziona:
- La testa fresante monta degli utensili chiamati cutters, che sono dei dischi di acciaio e servono a demolire la roccia. Poi ha altri utensili, chiamati scrapers, che servono a prendere la roccia abbattuta e a caricarla sul nastro che la porterà all’esterno.
- Con questa lettera ho indicato i pistoni di spinta dello scudo primario. Questi sono i diretti responsabili dello scavo e dell’avanzamento della macchina.
- Questi altri pistoni servono a impedire che la TBM ruoti su se stessa come avviene quando fate un buco nel muro col trapano: ad un certo punto la punta si blocca e la forza del trapano ve lo fa girare tra le mani. Lo stesso avverrebbe alla TBM senza questo dispositivo.
- Un altro dispositivo importante sono i grippers. Sono due pannelli metallici che vengono spinti lateralmente verso la galleria e servono a bloccare la TBM e permettere ai pistoni B di avanzare. Questo serve a rendere indipendente il movimento dei due scudi, che si muovono allungandosi ed accorciandosi un po’ come un verme.
- Sono altri pistoni idraulici, detti di spinta secondaria. Si utilizzano quando si incontrano terreni così poco resistenti che rendono impossibile usare i grippers (D). Allora per avanzare la TBM spinge direttamente, con questi pistoni, sul rivestimento definitivo che inizia alla fine dello scudo secondario.
- Infine c’è l’erettore, cioè il braccio meccanico che serve ad alzare e posizionare i conci prefabbricati che costituiscono il rivestimento della galleria.
- I carri di back-up sono disposti in coda alla TBM e sono lunghi anche più di 100m.
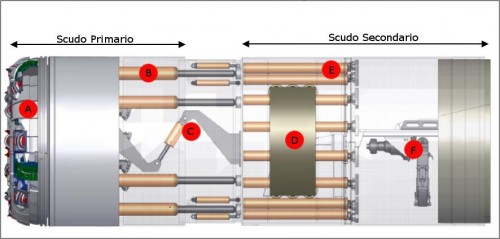
Qualche differenza importante:
- Il sostegno del fronte: Le EPB sono state messe a punto per lo scavo di terreni soffici a piccola profondità (per esempio le metropolitane nella pianura padana) e quindi oltre alla forza esercitata dalla testa sul fronte (questo avviene in tutte le TBM) queste macchine sono dotate di un sistema di iniezione di acqua, aria o fanghi che serve a non far perdere consistenza al terreno e a non farlo crollare.
- Uno, nessuno o due? Gli scudi: servono a proteggere la macchina e gli operai da eventuali crolli di roccia. Dove si è certi della compattezza dell’ammasso si potrà scegliere una macchina aperta, cioè senza protezioni. Dove invece si prevede di attraversare rocce molto fratturate o, addirittura, delle faglie, si useranno le TBM scudate. E due scudi non vuol dire uno sopra l’altro per reggere di più, ma si tratta di un sistema telescopico che si realizza tra il primo scudo (quello con la testa fresante) ed il secondo tramite dei pistoni idraulici e che permette alla fresa di avanzare anche se la roccia dovesse essere di pessima qualità.
Ed una curiosità: tutte le frese vengono battezzate con un nome femminile. Questa usanza non è di carattere grammaticale – la fresa – ma si deve alla credenza del passato che la presenza delle donne in miniera fosse portatrice di sventura; la credenza, divenuta ormai solo una tradizione, viene perpetuata nei moderni cantieri ed alle frese si assegnano, scaramanticamente, sempre nomi di donna. Allo stesso modo troverete sempre la statuina di Santa Barbara, protettrice dei minatori, collocata all’ingresso di ogni galleria durante tutto il periodo dei lavori.
Per oggi credo di avervi raccontato abbastanza… Posso solo aggiungere che la scelta tra un sistema di scavo ed un altro è legata a moltissimi fattori. In linea molto generale possiamo dire che se la previsione geologica è fatta davvero bene lo scavo con la TBM è molto più veloce e sicuro dell’esplosivo, ma se c’è qualche imprevisto si corre il rischio di bloccare la fresa e, come successo qualche volta, di doverla abbandonare in galleria e cambiare percorso.